The final assembly process is a critical stage in manufacturing, ensuring that all components are correctly integrated and fully functional before the product reaches the customer. This process involves several key steps to guarantee the highest quality and reliability.
By following these meticulous steps, manufacturers can ensure that the final product is of the highest quality, fully functional, and ready for delivery to the customer.
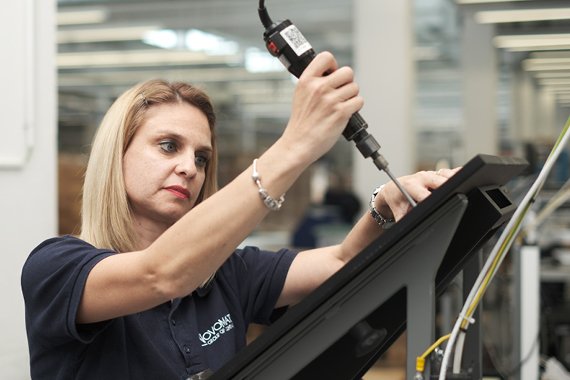
Final Assembly
During this stage, all individual components and subassemblies are brought together to form the complete product. This step requires precision and attention to detail to ensure that each part fits perfectly and functions as intended.
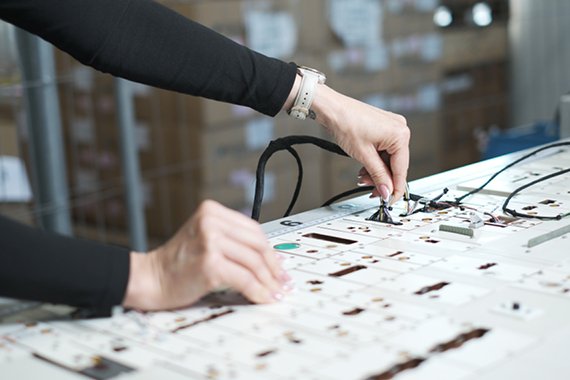
Functional Check
Once the final assembly is complete, a comprehensive functional check is performed. This involves testing the product to ensure that all features and functions operate correctly. Any discrepancies or malfunctions are identified and rectified at this stage to prevent defects from reaching the customer.
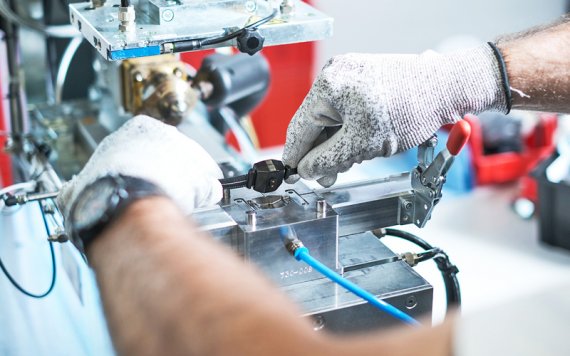
Push-Pull Inspection of Contacts
The next step involves a push-pull inspection of electrical contacts. This test ensures that all connections are secure and can withstand the mechanical stresses they may encounter during use. Proper contact integrity is crucial for the reliable performance of the electrical system.
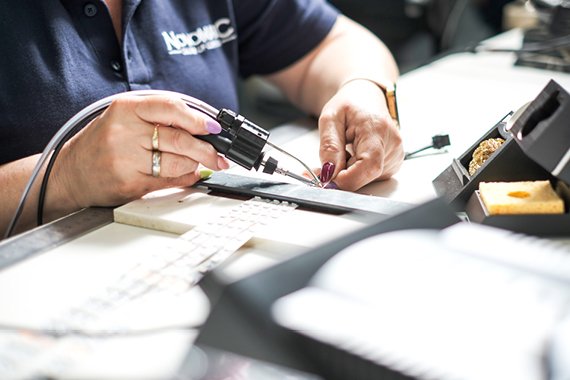
Final Electrical Inspection
The final step in the process is a thorough electrical inspection. This involves testing the product's electrical circuits to ensure they meet all specified requirements and standards. This inspection verifies that there are no short circuits, open circuits, or other electrical issues that could affect the product's performance or safety.