The process of manufacturing a product involves several detailed steps to ensure quality and precision.
The initial phase is planning, which includes CAD planning where detailed designs are created to outline the product specifications. Comprehensive documentation is prepared, including cutting lists and layout plans for the lay board. Sampling is conducted to create prototypes, validate the design, and make necessary adjustments.
The next step is automated crimping, which involves a fully automated process for cutting, stripping, and crimping cables ranging from 0.14 to 6mm². The cables are first cut to the required lengths, then the insulation is stripped from the ends. The exposed ends are crimped with connectors, and for certain cables, a semi-automated crimping process is used to ensure precision.
This is followed by partial assembly, where connectors are assembled and applied to the cables. Components are soldered to ensure strong electrical connections, and injection molding is used to encase components in plastic for protection and durability.
Wire harness assembly is the next step. Cables are bundled together for organization and protection through wrapping. Shrink wrapping is applied for additional mechanical protection and insulation, ensuring that the wire harness is secure and durable.
Finally, the product undergoes a final inspection. This includes a functional check to ensure proper operation, a push-pull inspection of the contacts to test the strength and reliability of the connections, and a thorough electrical inspection to ensure that all connections are secure and functioning properly.
This structured approach ensures that the final product meets all quality standards and customer specifications.
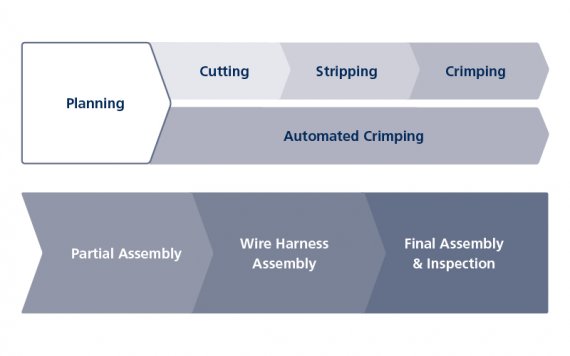
An overview of our production process
1. Planning
- CAD Planning
- Documentation (cutting lists, layout for lay board, etc.)
- Sampling
2. Automated Crimping
(Fully automated cutting, stripping and crimping (0,14-6mm2)
- Cutting
- Stripping
- Crimping (Semi-automated crimping of cables)
3. Partial Assembly
- Assembly and application of connectors
- Soldering
- Injection Molding
4. Wire harness assembly
- Wrapping (bundling)
- Shrink wrapping (heat and mechanical protection)
5. Final Assembly
- Functional check
- Push-pull inspection of contacts
- Final electrical inspection